Atlas Copco Compressor Technique
Atlas Copco Compressor Technique a world-leading provider of sustainable productivity solutions. Customers benefit from innovative compressors, vacuum solutions and air treatment systems, construction and mining equipment, power tools and assembly systems.
FX REFRIGERANT AIR DRYERS
.png)
Dry, quality air is vital for long-term, troublefree operation of your processes. Atlas Copco’s FX dryers protect your products and systems against damage or corrosion.
They remove moisture from compressed air with a dew point as low as 3°C/37,4°F. Easy to install, simple to operate and reliable, they provide the dry air you need, allowing you to concentrate on your core business.
Solid performance
- Steady pressure dew point
- No freezing of condensed moisture
- No chance of moisture entering the compressed air system.
Simple reliability
- Quality components, generously sized
- Simple and proven design
- Effective control system (hot gas bypass).
Easy Installation
- Plug and play concept
- Single electrical connection
- All units pre-commissioned
- Self regulating.
Minimal maintenance
- Long service intervals
- Few component replacements
- Ergonomic design for fast access to key components.
Significant cost savings
- Increased reliability and lifetime of tools and equipment
- Reduced pipe work leaks, meaning reduced energy bill
- Fewer repairs to tools, machines and pipe work
- Less inconvenient breakdowns and stoppages
- Minimal chance of product spoilage through moisture carryover.
Oil-injected Rotary Screw Compressors
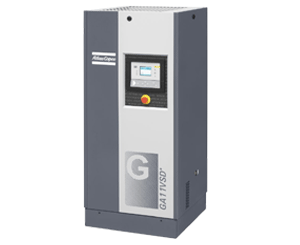
Atlas Copco has turned the compressed air industry on its head by redesigning the conventional layout of a typical air compressor. Instead of the normal space-taking horizontal design, the new GA 7-37 VSD+ has an upright, vertical, low footprint layout. This saves valuable floor and work space, eases maintenance access, accelerates manufacturing time, and reduces the total cost of ownership for all customers.
- Extreme savings
- No idling time
- Silent operation
- Small footprint
Efficient
- On average 20% lower Specific Energy Requirement (SER) than the current GA VSD models. Eco-efficient VSD+ reduces energy consumption by on average 50% compared to the current idling models.
- On top of energy savings, Free Air Delivery (FAD) increase of up to 12% over the range.
- Efficient fan motor (ERP 2015) reduces electricity consumption and noise levels.
- Highest motor efficiency (iPM), up to 96.8%, outperforming IE3 efficiency levels.
Reliable
- Low maintenance: fewer components, increased uptime.
- Worry-free: the GA 7-37 VSD+ has been extensively field-tested over three years.
- Based on unique combination of proven technologies and existing components,
Smart
- Elegant and revolutionary design
- Frequency-controlled operation as standard (VSD+), integrated dryer available.
- Fewer components & few options: impressive list of standard features.
- Ecological design, efficient material usage.
Compact
- Extremely small footprint.
- Clever design allows the GA 7-37 VSD+ to be placed against a wall.
- Robust: motor is oil-cooled; element rotor and motor have the same axis.
- Drive train: direct connection between element and motor.
- Very low noise level, with separate compartments for drive train and cooling.
Line Air Filters
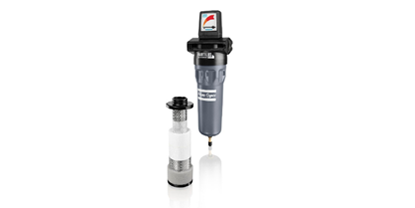
Atlas Copco’s UD+ filters efficiently reduce all types of contamination in your compressed air stream to protect your investment, equipment and processes. Thanks to its unique glass fiber filter media package, the UD+ offers a two-in-one filter technology, combining two filtration processes in one product. The UD+ offers the same reliability and high air purity as traditional filter packages (with two filters), but reduces pressure drops with 40% and saves space.
The UD+ is certified according to ISO 12500-1:2007 and ISO 8573-2:2007 standards by TÜV Rheinland and patents are pending.
Enhanced high-performance stainless steel filter cores
Enhanced high-performance stainless steel filter cores ensure ultimate strength and low risk of implosion.
Protection paper
Protection paper avoids direct contact between filter media and stainless steel filter core.
Epoxy sealed caps
Epoxy sealed caps for reliable filtration.
New, enhanced glass fiber media
New, enhanced glass fiber media ensure high filter efficiency, low pressure drop, and guaranteed lifetime performance. For oil coalescence filters, multiple layers are wrapped around each other to avoid the risk of early oil breakthrough.
Internal ribs
Internal ribs support the element and facilitate the route of oil droplets.
User Friendliness
Increased user friendliness and reliability via push-on element.
Double O-rings
Double O-rings guarantee proper sealing to reduce leakage risks and increase energy savings.
Dust filters
Dust filters the open foam acts as a pre-filter for the largest dust particles, which prolongs the filter lifetime.
Oil coalescence filters
Oil coalescence filters the double drainage layer (outer protection paper and foam) has a large drainage capacity which is ideal for variable speed compressors. Moreover, the poly-urethane foam avoids oil re-entrainment.
AIRNET
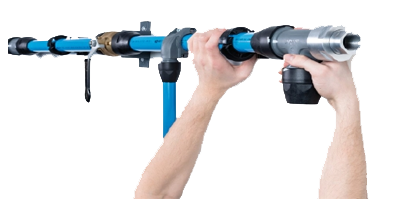
AIRnet is a compressed air piping system that delivers quality air exactly where you need it, from compressor to point of use.
AIRnet is a reusable aluminum piping system designed in line with ASME B31.1 / B31.3 to deliver a fast, easy, and reliable distribution network for Compressed Air, Nitrogen, and Vacuum.
TIME AND TOOLING
- Quick connections with no need to crimp, thread, solder or glue the pipe
- No heavy tooling or machinery required
- PF series can be connected to any existing network via simple use of adaptor unions and nipple sockets
- PF series is assembled by hand, a push of the pipe into the fitting is all it takes
MODULARITY
- Easy to handle and easy to work with lightweight materials
- Modular design supports extensions and modifications to meet new demands
- Components are interchangeable and reusable after disassembly
- Quickdrops are easily mounted, both horizontally and vertically
SUSTAINABILITY
- Optimized inner body design minimizes flow resistance and pressure drop in the fittings
- Low friction factor and seamless connections minimize pressure drops in the pipe network
- Superior sealing technology ensures a leak free system and maintains performance over time
- Durable and corrosion resistant materials offers a maintenance free system
SAFETY
- Safety factor of 4 for all diameters
- Camera control and automatic assembly guarantee zero defect manufacturing
- Plastic components and pipe clips comply to UL 94 HB and UL 94 V-2 for flammability
- Torque indicators ensure sufficient torquing
Oil Sealed Rotary Vane Vacuum Pumps
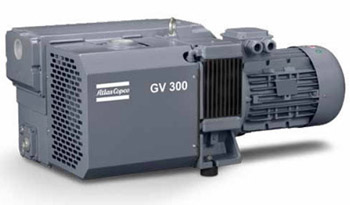
At Atlas Copco we have been developing state-of-the-art vacuum pumps for many years, utilizing our core technologies. We constantly aim to innovate, improve performance and target new application areas. The characteristics of our oil-sealed rotary vane vacuum pumps complement those that have made Atlas Copco the stand-out worldwide supplier of air solutions: high quality, impressive reliability and low lifecycle cost.
- Easy to install due to compact, space-saving design.
- High reliability through a rugged design and optimal oil retention at
all operating pressures. - Low maintenance and wear due to optimally selected shaft speeds.
- Low noise and vibration levels throughout the pressure range.
Robust Technology
The GV 18-300 series operates according to the proven oil-sealed rotary vane principle that has been successfully used for many years in all general vacuum applications of industry. The GV 18-300 series is a robust and highly regarded product coming from a technologically advanced market leading design.
Innovative features
Atlas Copco has packed the GV 18-300 range with innovative features that ensure the highest possible performance at the lowest possible lifecycle cost. The built-in gas ballast is fitted as standard to assist in water handling capability. Other integrated functions include the lubricant retention and return mechanism which means that these machines are suitable for continuous operation between 400 mbar(a) and their ultimate pressure.
Clean and efficient
The oil separation circuit of the GV 18-300 has been optimized to minimize oil vapors in the exhaust gas. The inlet non-return valve protects the vacuum pump against counter rotation in the event of stopping without venting. This device also protects the point of use against back sucking of oil.
PSA Nitrogen Generators
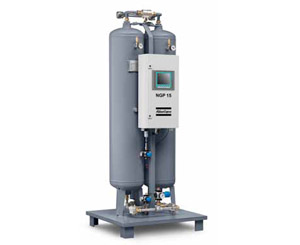
Atlas Copco’s new nitrogen generator uses Pressure Swing Adsorption technology to isolate nitrogen molecules from other molecules in compressed air. Oxygen, CO2, water vapor and other gasses are adsorbed. The result is virtually pure nitrogen at the outlet of the generator. The NGP series are a very costefficient source of nitrogen used in various industries like food and beverage, metal processing, electronics, and many others.
Ready to Use
- Only requires a supply of dry compressed air
- Plug-and-play
- No specialist installation or commissioning
- Fully automated and monitored including oxygen sensor as standard
- Performance guaranteed independent from temperature
Cost Savings
- Low installation and running cost – highly efficient technology
- No additional costs such as order processing, refills and delivery charges
- Virtually service free
- Quick pay back – often less than a year
Exceptional Convenience
- Continuous availability (24 hours a day, 7 days a week)
- Risk of production breakdown due to gas running out is eliminated
Desired Purity
- Nitrogen supply according to your need: from 95% to 99.999%
- Very easy to set up the device for other purity levels
High Flow Capacity
- The wide product range and nitrogen flows up to 1100 Nm³/h make the new NGP series ideal for applications such as food processing, pharmaceutical, metal industry, oil & gas, marine, packaging and many more.